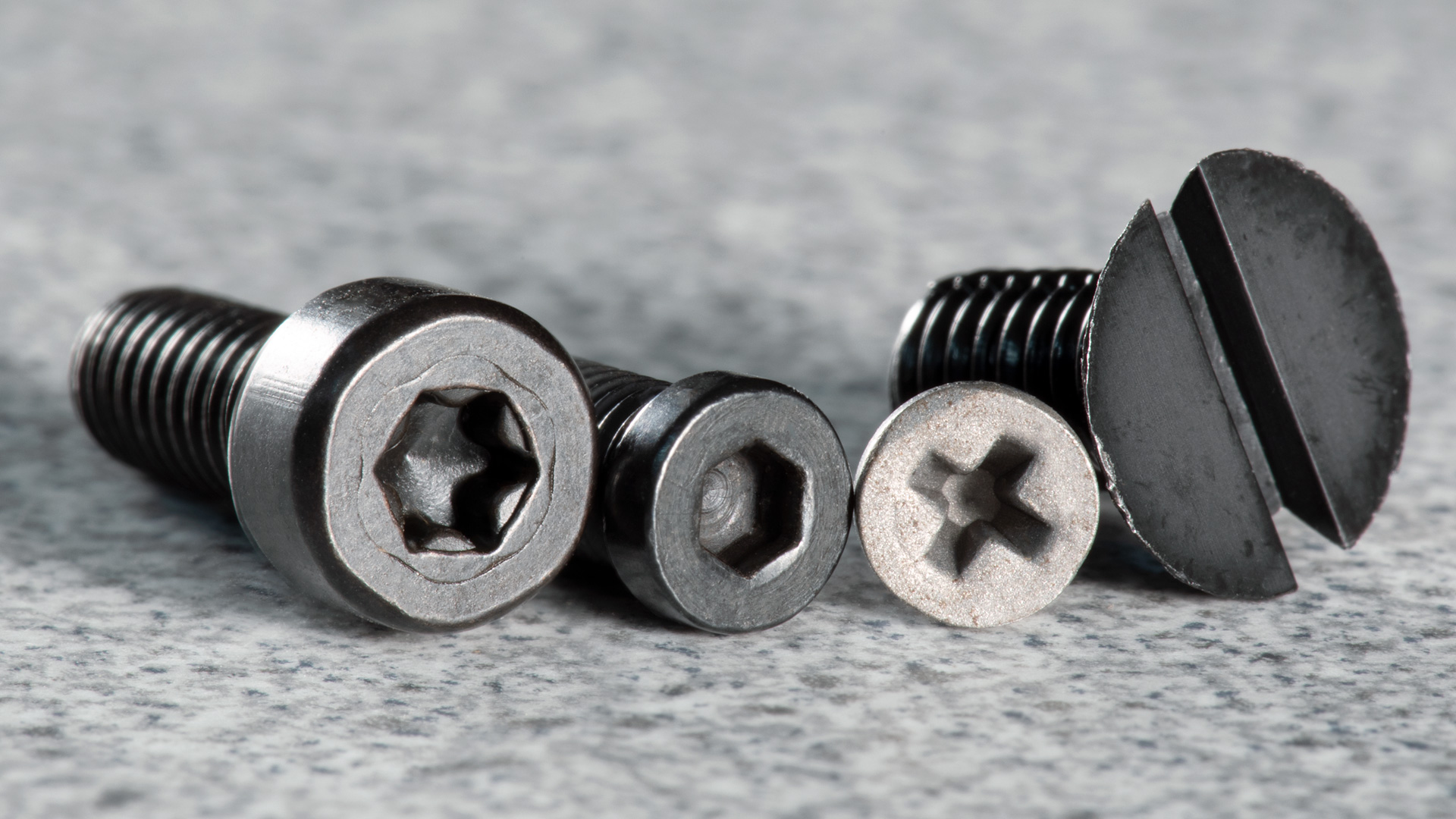
I am old enough to remember when guns had slotted-head screws for almost every purpose and application, perhaps with the exception of Phillips-head screws to attach buttplates and recoil pads to shotguns and rifles.
These days, if you look at handgun grips alone, you have slotted screws, Phillips screws, square-notch screws, Allen/hex screws and torx screws, all doing the same thing. Not only that, but some companies also make guns with different types or sizes of screw heads when the threaded portion of the screw served the same or similar purpose.
Are the gun companies doing this on purpose? Do their design engineers not speak to each other? Or are there other reasons in design, manufacturing or sales that drive the use of the different screws now so common when once upon a time a simple slotted screw served the purpose of attaching parts together quite nicely?
Grumpy, Detroit, MI
There are a number of possible answers to the questions you pose, although I will not pretend to know all of them.
Slotted screws have been the most popular over the years because they worked, and they were inexpensive to make. The key thing to keep in mind is that a slotted screw is designed to be tightened and loosened with a properly fitting screwdriver that closely fits the length, depth and breadth of the slot for maximum effective torque in tightening or loosening the screw in its operational location. Hollow-ground screwdrivers, in different sizes, were developed as tools to specifically fit the various sizes of screws used in manufacturing firearms. They worked quite well when matched up with the proper slot for which they were designed. However, many end users, owners and operators chose a hardware-store screwdriver designed for carpenters and plumbers as a replacement for the correct tool. This invariably resulted in damage to the screw and, in some cases, the area of the gun around the screw when the ill-fitting screwdriver blade slipped from the notch of the screw being turned and scarred the finish of the part.
Phillips-head screws, by design, have a natural propensity for centering the screwdriver bit in the driving surfaces. They also create a camming action, limiting the amount of torque that could be applied to the screw before the contact surfaces lost traction and slipped—in essence preventing overtightening the screw. When installing and removing recoil pads, for instance, the position of the screw head is often not seen because of its enclosure within the pad itself, making the natural centering effect of the Phillips screw a welcome benefit. Added to that is the inherent camming action of the Phillips screw makes overtightening and damaging the wood stocks to which recoil pads are attached much less likely.
I have seen no widespread use of square notch—or Robertson-head screws as they also known—in firearms. Although I have seen grip screws with enclosed, four-sided slots configured in that fashion on custom guns, I am unaware of any of the major manufacturers using these parts as fasteners.
The original idea was to allow the tool operator and/or machine to apply maximum torque to the screw with minimum slippage in a repeatably consistent manner.
Hex- and Allen-head screws both have six sides to the opening for the tightening tool (sometimes it is referred to as a key) to be inserted. These screws are the same for all intents and purposes. They can be considered the same item with a different name in the firearm arena. It is common to use the same keys or bits of a similar size to apply or remove torque while turning a hex or Allen screw.
Torx screws are splined, having six ridges within the slot opening for engagement with the proper-fitting torx bit. The splined design maximizes the amount of torque that can be applied to the screw without slippage or rounding off the edges of the softer part, whether it be the screw or the adjusting tool. With rare exception, the torx screw allows the tool user to apply maximum torque to the fastener being used to join two or more parts.
In my educated opinion, having worked in the firearm industry for more than a few decades, one of the main reasons for changing screw slot patterns is to force the user, operator or technician to use the proper tool when applying torque in either direction to the screw. This lessens the likelihood of the screw or surrounding area from the possibility of damage by using the wrong tool.
Bear in mind that gun companies are in business to make money, not necessarily to make sense to the consumer. Rest assured that all the major manufacturers put a lot of effort into turning out the best product for the highest profit margin possible, and yet satisfy the customer demand to meet their sales goals on a continuing basis. As long as these parameters are met, dialog between their engineers, manufacturing team and sales associates is really moot, although it hardly makes sense to everyday people like you and me.