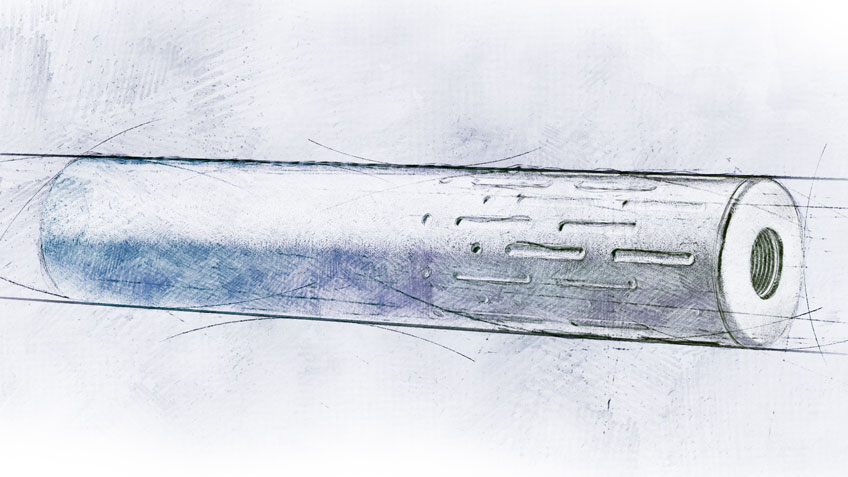
Let us assume for a moment that you are an old hat at the sound-suppressor game. As a veteran of the NFA registration wars, you have been fingerprinted and had your mugshot taken (in duplicate), survived the six- to 12-month wait and have the tax stamp, gray (or lost) hair and lightened wallet to prove it. You can recite the benefits of suppressed-rifle shooting better than a tactical-pants-wearing industry sales rep.
So, when was the last time you detail-cleaned your suppressor’s mounting surfaces? Was that keyhole-shaped aperture in your blast baffle there when it was new? Which bullet weights are unsuitable for suppressor use with your rifle? Why are you looking at the ground and shuffling your feet? If you have not already learned that simply attaching a can to your rifle and shooting it without further care eventually leads to problems, trust me when I say that you will. I encounter enough neglected suppressed rifles throughout the year to know that a little chalk-talk may be helpful.
The first tangible things that a new suppressed-rifle shooter experiences are the effects of all that pressure bottled up in the bore longer than usual. In manually-operated actions, this “back pressure” goes largely unnoticed until cleaning time. Semi-automatics are a different story, sprinkling shooters’ faces with gases, gunk, carbon and unburnt (or burning) powder granules that rocket through ejection ports and receiver gaps. This pressure also speeds up our rifles’ cyclic rates and deposits an inordinate amount of fouling into the chamber, gas system, magazine and receiver(s).
The most-effective way that I know of to reduce these problems is to use an adjustable-gas system. Whether suppressed or unsuppressed, the goal is to use the minimum gas required for your semi-automatic to feed the next round and lock back on an empty magazine, if so designed. Many aftermarket direct-impingement, adjustable-gas blocks are available for retrofit. Look for those with click adjustments and ensure they fit your barrel’s outer diameter (and under your handguard) before ordering. Rifles with piston-operating systems often have their own proprietary gas blocks that limit you to the rifle-manufacturer’s products, but fortunately they usually come from the factory in adjustable configurations.
Adjustable-gas tubes and bolt-carrier groups are also available for easy retrofitting. While they do not typically match a gas block’s capabilities, these drop-ins may still provide the needed tuning to slow down your bolt carrier and reduce fouling in the rifle while shooting suppressed. The more settings an adjustable-gas system has between wide-open and fully closed, the better.
Ammunition companies offer subsonic loads in many common centerfire-rifle chamberings, with .300 BLK/Whisper being the most common due to its ability to reliably cycle semi-automatic actions. But, just because a particular load is marketed for suppressed guns does not ensure it is right for your rifle. So-called, subsonic “cycler” loads rely on heavy-for-caliber projectiles to help generate the pressure required to operate a semi-automatic.
Those bullets are often too long for conventional twist rates. For example, the typical 1:10-inch twist rate used in modern .30-caliber rifles is not tight enough to fully stabilize the popular 200- to 220-grain, .30-caliber projectiles used in .300 BLK and 7.62x39 mm subsonic loads. This does not mean you need a barrel change to shoot subsonic ammo. Rather, you should use caution when firing these projectiles through a suppressor. If your bullets are wobbly out of the bore, they stand a good chance of impacting and damaging your suppressor’s internal structures.
A friend recently bought an expensive box of 5.56 NATO “Tactical Cycling” subsonic ammunition loaded with 112-grain projectiles. I recommended he perform a simple test to determine whether or not they would stabilize in his 1:8-inch-twist barrel before sending them through his suppressor. My experience is that if you have nice, round holes up close, the suppressor will be fine, even if there is some instability at longer distances.
But, elongated holes or sideways bullet profiles on targets just a few feet downrange are indicators of major stability problems. Firing unsuppressed into a paper target at 7 yards showed his long-for-caliber bullets were tumbling end-over-end at close range. He decided against risking suppressor damage. If your rifle’s twist rate is not ideal for heavy, subsonic bullets, you can still shoot traditional-weight bullets loaded to subsonic velocities, hand cycling them as you go.
Back when sound suppressors were not widely issued within the U.S. military, maintenance knowledge was as scarce as the desire to clean them. Suppressors sometimes became permanently attached due to rust, heavy carbon or having melted into an unintentionally welded mess. Those cans often had to be cut off, which had the effect of making one equally unpopular with the armorers and the command group.
Several customers’ rifles have come in to my shop with suppressors stuck in place, usually due to excessive carbon. That same carbon can contribute to improper lockup of a quick-detachable suppressor, creating an unsafe condition. Ratchet-toothed mounts will fail if carbon is allowed to build up and harden between the teeth. I recently chided the owner of one such mount and he candidly admitted his suppressor had been launched downrange for this very reason. A bit of scraping followed by a few minutes on a wire-wheel was all it took for me to return his alloy steel mount back to like-new condition.
In the Army, we tried everything from the self-cleaning/no maintenance farce to frequent solvent tank scrubbing followed by compressed-air drying in order to keep the early QD designs working. For some reason we even tried to ream out our rifle cans using hand-drill-mounted chamber brushes. None of those methods worked well, but one that did still works for my centerfire-rifle suppressors today: Clean the rifle and suppressor-mounting surfaces and inspect the baffles and bore regularly. I use bore solvent or mineral spirits on a toothbrush or wire brush (depending on the level of carbon buildup) on mounting surfaces—including those inside the suppressor—then wipe it clean and apply a light oil or thin grease coating. Spend extra time cleaning your rifle’s chamber, locking-lug recesses and receivers after suppressor use.
After cleaning your rifle and mount, look into both ends of your suppressor with a good light. If you see nicks on the blast baffle, baffle stack or end cap or any damage to welds, make arrangements with the manufacturer to have it fixed before using the silencer again. If your can is designed to be disassembled, take advantage of that capability to clean and inspect all components effectively. Take care of a suppressor, and it will do its job.