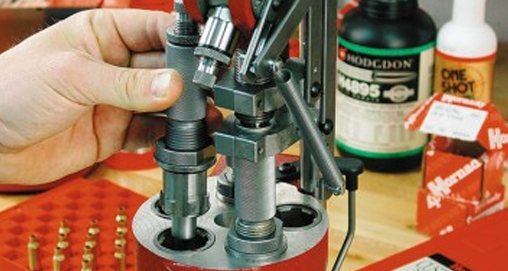
While a federally subsidized crate of ammo might sound appealing, it'll never happen. If it did, lead-free bullets, justification for every round, ATF approval and a special tax would be the price. What I'm talking about is a progressive reloading press. I've been presenting handloading seminars at the NRA Annual Meeting and Exhibits for the last three years, and in other venues on occasion. There are a lot of handloaders and the ranks are growing, but many with whom I talk don't use progressive equipment.
Progressive presses are a lot more expensive—about three to four times more than single-stage presses. They use the same dies, but require a different shell-holder plate for each cartridge unless they share the same rim diameter, like say, the .308 Win. and the .45 ACP. Plates are about $30 each, so it's not just the press that costs more.
Aside from that, there's not much difference in dollars spent, and I've found I can load about eight to 10 cartridges on my RCBS Pro 2000 Progressive press for every one I load on my single-stage Rock Chucker press, even when using the electronic Chargemaster powder dispenser. The ability to swiftly churn out ammunition is the appeal of a progressive reloading system.
If progressive reloading interests you, there are some things you should know. When setting up a single-stage press, it's always helpful to set out several cases for the purpose of getting everything adjusted. With a progressive press, this process is a bit more complex and will usually consume about a dozen cases. Setup is critical with a progressive press—kind of like timing a car engine. You need to adjust each die individually and you'll also need to adjust the primer-seating tool and powder dispenser. One adjustment hiccup throws a wrench in production.
Progressive presses are great for straight-wall pistol cartridges because they require no lube. You can size them, prime them, charge them, expand the case mouth and seat a bullet with no interruptions. Bottleneck cases have to be lubed just like when using a single-stage press and the only way to do this, while taking advantage of the progressive press' speed, is to use a spray lube like Hornady One Shot or RCBS Case Slick.
Sometimes you must trim rifle brass and this must be done after sizing, so it interrupts the progressive process. Most often, I load rifle cartridges for performance rather than quantity. I generally size them on the single-stage press and then check for length uniformity and neck concentricity. After that, I'll discard unsatisfactory cases, trim if necessary, tumble and chamfer case mouths. The cases are then ready for the progressive press where they can be primed, charged and topped off with the bullet of choice without interruption.
A critical aspect of using a progressive loader is charging the case with powder. While methods differ from press to press, the function is similar. A volume powder dispenser cavity receives a charge of powder from the hopper. When the case is forced into the dispenser by the press, it activates the dispenser and the captured charge is dropped into the case. When the press handle is lowered, another volume charge is picked up. Cylindrical powders like IMR 4895 can bind the mechanism, interfering with volume measurement.
For this reason, I only use ball or flake powders like Ramshot TAC or Hodgdon Longshot with the volume measures on progressive presses.
I also like to bracket my charge weight in accordance with the maximum dispersion deviation of about 10 samples, especially when working with maximum or near-maximum loads. For instance, I'll charge 10 cases and weigh the charge in each case. If the maximum deviation is, say, .4 grains, I'll adjust so it averages .2 grains—half the deviation—below my desired charge. You'll have to experiment with this, because some powder measures and some powders work together better than others.
Ideally, you can set your progressive press beside your single-stage press like I did with my two RCBS presses. If you only have room for one press, the RCBS Accessory Base Plate will let you swap any RCBS press or tool—like its case trimmer—that requires mounting. The reason I keep the single-stage press set up is because I use it for load development. I never "work up" a load with a progressive press. After I find a load I like, I'll switch the dies to the progressive press, get everything adjusted and go to town, as grandma used to say.
Can you produce accurate and consistent ammunition with a progressive press? Sure. The first trick is proper press adjustment. And, you need to remember progressive press operation is a bit more involved. Before each pull of the press handle, you'll have to rotate the base plate, insert a case and place a bullet on top of another case. Also, every time you run the press handle you have to run it both ways; down to use your dies and powder dispenser and up to seat a primer.
Ever heard the phrase, "Garbage in, garbage out?" The same is true with progressive presses. If you don't adjust and operate them correctly, garbage ammo is what you'll get.
A progressive press is a great tool that will save time and can make quality ammunition. Once you get one rocking, you might load so much, you'll get reloader elbow—a condition similar to tennis elbow that comes from working a press handle too much. Its hurts just the same, but will receive much more sympathy—at least from the crowd I run with.