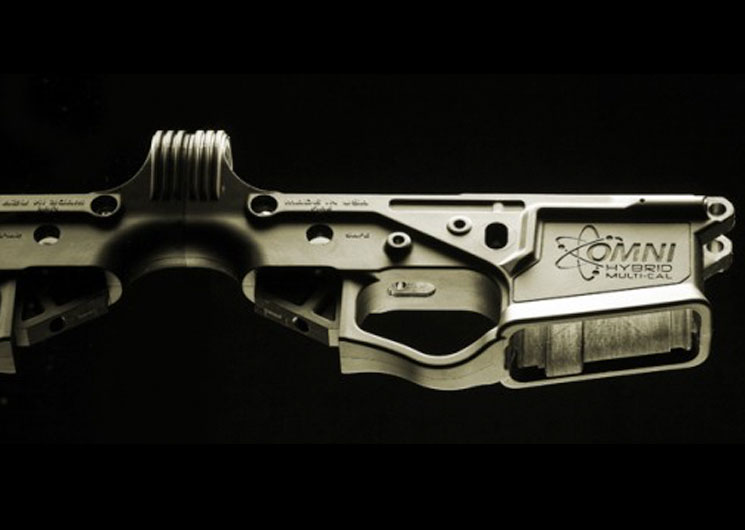
Synthetic materials have been used in firearms manufacturing since the early 20th century. Franzite was one of the first plastic-like materials that replaced hard rubber, wood and ivory grips for a wide variety of handgun models. These materials were relatively inexpensive, durable and could be formed into nearly any shape, texture, style and eventually, color. The lack of aesthetic charm was counterbalanced by practicality. By the 1950s, firearms manufacturers began using similar "space-age" materials for rifle stocks, pistol grips and fore-ends. Most of us have heard about the cool reception the original M16 received from troops forced to trade in their wood and steel M14s for the new aluminum and plastic, small-bore rifles. Heck, senior non-commissioned officers were still referring to them as "toy guns" when I joined the Army in the 1980s.
Up to that point, man-made materials had largely been relegated to supporting roles in the firearm world, but Glock changed that—and public perception—with its widespread use of polymer handgun frames. Traditionalists claimed polymer frames could never stand up to the same abuse as steel and aluminum, but we all know how those predictions played out. As long as the right metals are used in critical wear and bearing areas, polymer handgun frames go the distance.
The rifle world has been slower to incorporate polymers into main frame construction, and for good reason. Longarms tend to take a lot more abuse, at least in physically active shooting disciplines. More importantly, though, centerfire rifle cartridges can generate up to three times the pressure of the most common handgun loads, so receivers must be stout enough to support the barrels and barrel extensions that contain said pressure. Rifle receivers must allow mounting of optics—which may add considerable weight—support magazines holding up to 200 rounds and be able to withstand bending caused by recoil.
Modern rifles, like FN's SCAR and the Bushmaster/Remington ACR, employ lots of polymer, but those rifles were born in the polymer age and so benefit from being designed that way from the ground up. Not so with older guns like the AR family. The AR's upper receiver is fairly thin where it surrounds the steel barrel extension, making it a bad candidate for plastics where centerfire rifle cartridges are concerned. The lower receiver is another story though, and as a result, a few companies have eased polymer AR-15-size lowers into the commercial market.
When these units first hit the market, I wondered why anyone would want materials with no real track record when receivers made of forged or billet aluminum do the job nicely. Weight reduction would seem to be an obvious plus when switching to synthetics, but a forged aluminum 5.56 NATO AR lower's 8-ounce average weight is not exactly a scale tipper, especially when polymer lowers only shave a little off. Ounces do add up to pounds, however, so it is fair to say polymer is lighter than aluminum, even in beefier dimensions.
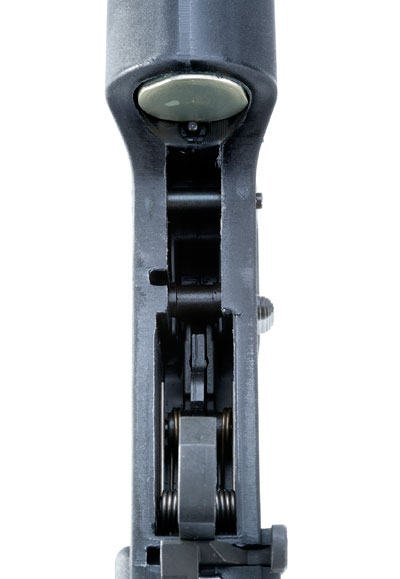
I found other advantages over the usual machined aluminum receivers, too. A reduction in cost is the most prominent, with polymer lowers running about one-quarter to one-half the price of machined-aluminum counterparts. But just as with weight, we are very nearly splitting hairs here. At the time of this writing, forged lowers may be found in the $60 to $120 range, but politics and world events can change that in a snap, and so the cost gap may once again widen significantly.
Another key advantage to molded receivers is customization. Tired of basic black? Color changes are a cinch. The range of options is limited only by the range of color additives. Bright colors and perennial favorites like flat dark earth, olive drab and gray can all be found in various forms. Since the color is added into the mixture during manufacture, it is part of the entire unit—when anodized or painted aluminum is scratched, raw metal shows through, exposing it to oxidation and corrosion in harsh environments. Scratches and gouges in polymer reveal more of what you see on the surface, so no touching-up is needed. Finally, the elastic nature of polymer makes it more resistant to damage from the type of hard use that can dent, bend or even crush aluminum receivers. Even the stiffest plastics have some "give" to them, which can be an advantage in today's rough and tumble world of fighting riflery.
BaggageSo, we can say polymer lowers are moderately lighter and cheaper, easily customizable in form and color and more scratch- and dent-resistant than aluminum receivers. Sounds like a good deal, but there is more to this story. One of the early lessons learned the hard way with these receivers was to use care when building a gun around them. A key weak point is the upper/rear portion of the receiver that is internally threaded for the receiver extension (aka buffer tube). Non-reinforced polymer receivers visibly flex in this area when tightening things up, and there is no real good way to support them while installing the tube. Over-tightening either a fixed stock's receiver extension or the castle nut for a collapsible stock can easily snap the polymer at this weak point, rendering the receiver useless. Some companies have beefed up their designs to account for this problem. If you find yourself installing a receiver extension on one of the non-reinforced lowers, I advise you to simply snug things up. A fixed stock's extension is not likely to loosen due to the way the buttstock locks into the recess on the back of the receiver. A collapsible stock's castle nut can be coated with Loctite when attached to the receiver extension and further staked to keep it tight.
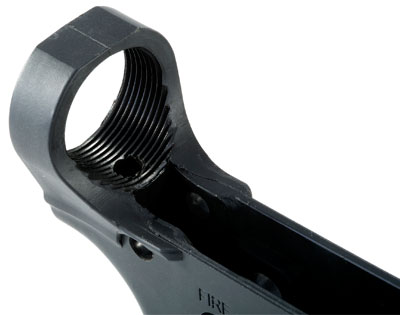
This is not the only point where flexing may occur in this particular material family. The lightest—and therefore thinnest-walled—polymer lowers flex in just about any direction. In fact, one of the lowers I tested for this effort was scarcely more rigid than a banana, easily bending in any direction.
The rear takedown and front hinge pins that connect AR uppers and lowers seem to be a common problem area with polymer receivers. The pins in three of the four lowers I worked with were either too tight or too loose. It seems the manufacturers have difficulty in maintaining the proper upper and lower receiver interface dimensions, which is a problem not commonly seen in aluminum AR receivers. I also found fit concerns with some small internal parts. Steel pins tend to walk their way out of their polymer holes. If the receiver's design has no provision to retain these pins, the shooter must be diligent about checking to ensure everything stays in place and lined up during firing.
A final complaint I have is not actually with the receivers, but rather with the lower receiver parts sometimes included with polymer lowers. A while back, I repaired a polymer AR lower that was having functional problems in the trigger group. When I opened it up, I was horrified to see that most of the pins and internal parts—including most of the trigger assembly—were made of plastic. Even the sear engagement surfaces were a polymer and steel mix. I thought I was looking at Airsoft gun parts, but it turned out to be parts actually shipped with a legitimate 5.56 NATO lower receiver. I could actually bend the hammer with my fingers. I gutted the innards, replacing them with proper steel parts, and that carbine has had no further troubles.
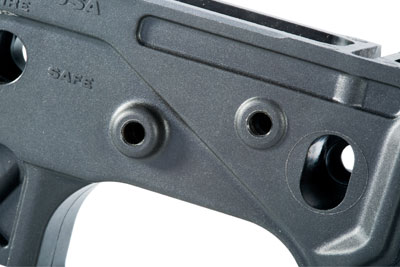
Branding
Last summer, I bought three different polymer AR stripped lower receivers to get a feel for ease of assembly and function. All were 5.56 NATO-size variants and came through distributors (rather than direct from manufacturers). Actual MSRPs are hard to find for these things, so I have included a street-price range here to show what you are likely to find them selling for. The three receivers are quite different from each other in form and, as it turns out, function, too. Obviously, a quick check online will produce other options and variations from these depicted here, but I think I grabbed a decent cross-section of available lowers.
Final Verdict?
I am having a hard time passing judgment upon polymer AR lowers, especially since I have only seen a handful of them. While a sample size of three lowers gives a range of options, it is generally too narrow to allow judgement to be passed on the category as a whole. As a consumer, if I were looking for one light, inexpensive lower on which to build an AR, polymer would be an appealing option so long as I did not mind making the necessary fit modifications. Retired Special Operations Forces operator John McPhee of SOB Tactical has been using a New Frontier Armory LW-15 in his training course for two-and-a-half years. Since I replaced the plastic internal parts used in the polymer lower on his rifle, he has put approximately 10,000 rounds through it without any trouble at all.
I bought all three lowers tested for this review off the commercial market, so I plan to modify them slightly to work for me over the long haul. Each of them can benefit from some tweaking to their upper/lower fit, and if I can make the GWACS model work, at least the money I spent will be put to some use as a learning experience. Looking at the group as a firearm manufacturer, the positives of polymer AR lowers do not sufficiently offset the negatives to incorporate them into even my lightweight production models at this time. Maybe someone will step up to the plate and offer a high-quality design that sufficiently addresses the fit problems while making the most of polymer's advantages, or possibly another option of which I was unaware may become available. Until then, I will continue to pay a little more for aluminum receivers.
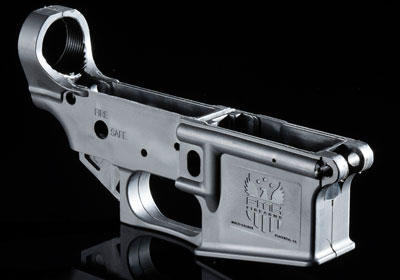
FMK Firearms AR-1
The FMK specimen was as simple as it gets. It is nothing more than a polymer clone of a Mil-Spec forged aluminum AR lower. It is made from a "high-impact composite polymer" and the claim that it "bounces back to shape" when most lowers bend or break is not an exaggeration. The threaded portion for the receiver extension is not reinforced, so the aforementioned care is needed while assembling the lower. This receiver was so flexible, when I fired prone off a 30-round magazine, I could tilt the upper to one side, away from the lower. The degree of upper/lower separation was not enough to induce a malfunction, but it was easy to see the widening gap when I applied some torque. The takedown and hinge pins were initially very hard to seat in the upper receiver, but once in felt very snug. Fifty rounds later, the front hinge pin became loose and stayed that way, with lots of slop between upper and lower at this critical union. The condition did not improve with further testing, but its actual function over a couple hundred rounds was flawless.
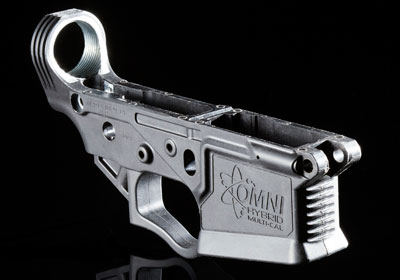
ATI Omni-Hybrid
The Omni-Hybrid lower receiver caught my eye at the 2014 SHOT Show. ATI used the polymer manufacturing process to exercise some creative juices, beefing up the receiver side-walls and trigger guard, flaring the mag well and adding some texture and good aesthetics into the mix, too. The trigger and hammer-pin holes also have added material around them. These raised gussets leave the pins seated deeply on either side and require flush fitting setscrews (provided) to hold them in position. While this may seem to be an extra worry, it really secures the trigger and hammer pins well, and none of the four setscrews came loose during testing.
The most notable enhancement to the Omni-Hybrid's design is the aluminum insert molded into the receiver's buffer-tube thread section. The large reinforcing piece made installation of the receiver extension easy, and no excessive flexing was noticed when I tightened the castle nut. Unfortunately, the Omni-Hybrid also suffered from upper-alignment problems. I tried multiple uppers on this lower and though all mounted and functioned, "shotgunning" them, or removing the rear pin only for maintenance, was very difficult. I found it easier to remove both the front and rear pins, separating the two for cleaning. The pins themselves are also hard to seat and unseat, due to binding with the upper. Function was flawless using multiple uppers on the Omni-Hybrid lower.
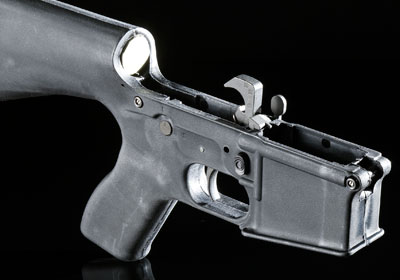
GWACS Armory CAV-15 MKIII
The CAV-15 polymer lower incorporates a lower receiver, fixed stock, pistol grip, trigger guard and receiver extension into one solid unit formed by two pieces bonded together. This clamshell design was originally marketed by Cavalry Arms and was quite popular when it first hit the market. The 10.25-inch length-of-pull stock houses a molded-in tunnel sized for a standard A2-length buffer and spring. Since the stock is fixed, the buffer-retainer pin and pin spring have to be held in place by a provided roll pin. Once you figure out how to hold the buffer retainer pin down far enough to get the sideways roll pin over it, driving the roll pin in place is not that hard.
The fixed grip eliminates any provision to install the selector detent and spring in normal fashion from the bottom. Instead, you have to install the spring from the top, followed by the selector detent (pointed up), then depress them while working the selector in from the side to hold them in place. I always wear eye protection in the shop and this is one case where it paid off. It is not hard to launch the selector detent straight up, but after a couple tries I was able to get everything in place. Unfortunately, the selector rotates rather freely beyond its detent stops, regardless of whether the hammer is cocked, which is not exactly the safest design.
Another departure from standard AR lowers is the CAV-15 MKII requires the use of captive takedown pins, because there are no holes for takedown-pin detents and springs. I bought a set of KNC push-button pins that use ball detents to hold them in place. Inserted left to right, they are a real bear to work with in this lower. When fully inserted, my fingers could not get enough purchase on the pin heads to push the buttons while pulling the pins to remove them. I had to mount the lower on a vice block and push from the other side at the same time with a punch.
That was the least of my problems with the GWACS receiver. Not one of the four different 5.56 NATO uppers I tried to attach fit this lower. They were all from different manufacturers and fit standard 5.56 NATO lowers without trouble. The misalignment of the upper receiver's pin tabs and the lower receiver's holes was evident and could not be fixed without removing significant polymer from the lower, elongating those holes in the process. This was an "out of box" test, so I elected not to do that. In each case, once the front pin was driven into place attaching the upper and lower, the rear pin was well off center. The upper pin then seized in place and had to be driven out—hard—in order to free the two receivers. Inserting the rear pin first made no difference with the alignment problem. I do not know if GWACS simply had a bad run of receivers, but my lower was non-functional out of the box.
The two most redeeming features of the CAV-15 design are its light weight and low cost when compared to an aluminum 5.56 NATO lower with stock and grip assemblies added. Those good points were small benefits, however, when balanced against the problems I encountered.