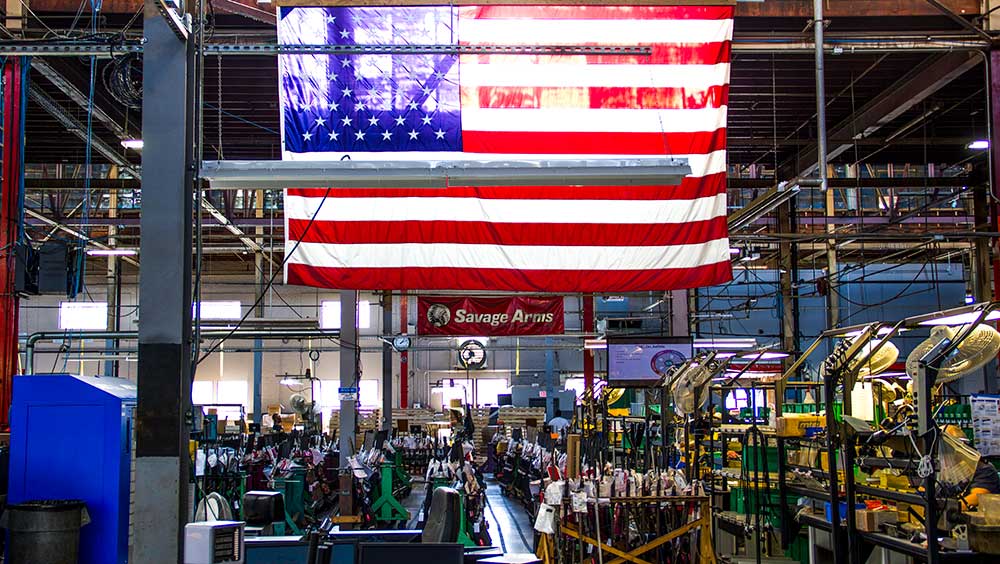
"Savage bought Savage"
When the “new” owners of Savage Arms visited NRA headquarters in September, 2019, this was the very first slide of the official presentation. Savage understood that, as a company with 125 years of history, one of the big questions on everyone’s mind would be, “who is this group that just bought Savage?” As it turns out, it’s a group that has been managing the company for many years now, and while this means there won’t be any dramatic changes, it also doesn’t mean the company will necessarily be following the same mold. Any changes that come will be market-driven, with the company’s legacy—and future—in mind.
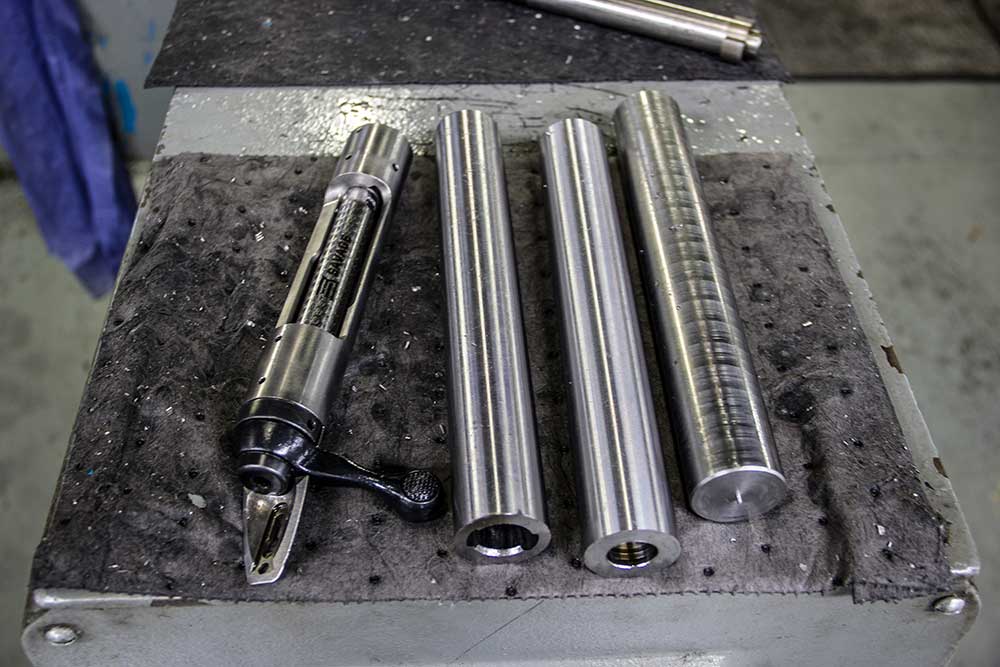
Al Kasper, the new President and CEO of Savage Arms, is passionate about the company and the people that comprise Savage Arms. Walking the factory floor with him, it’s abundantly clear that this is more than just idle talk: *Everyone* knows Al. Every station we visited, Kasper knew the name of the person operating the equipment, knew the function of that particular station and what the preceding and following stations included.
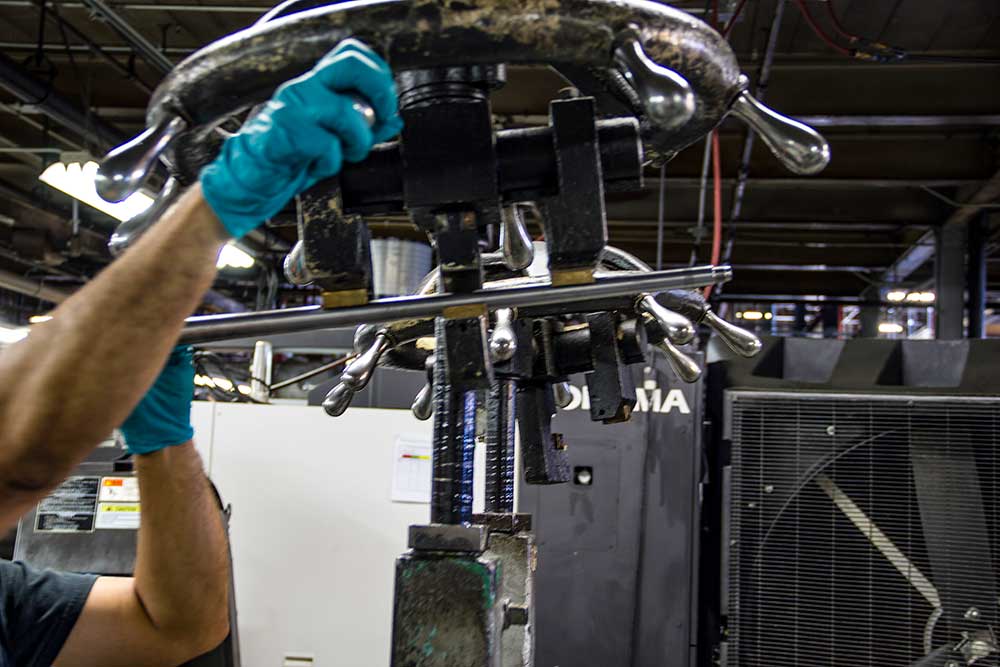
Kasper has 23 years with Savage, through three different, private-equity firm ownerships and one public company. He made it abundantly clear that the new investment group he assembled to buy Savage is in this for the long haul - this is not a quick turnaround for resale by any means. The group intends to keep Savage growing organically with potential acquisitions.
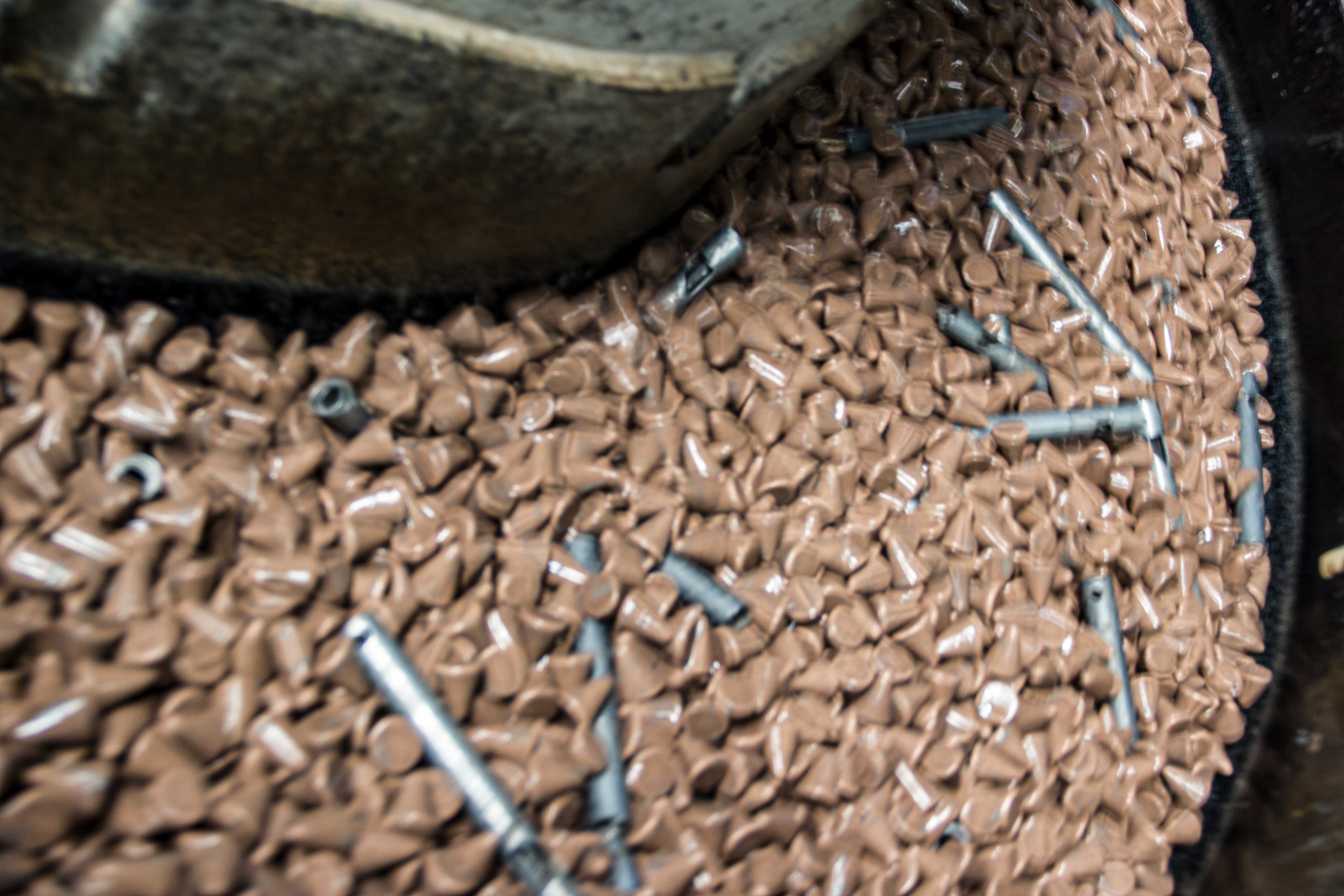
This isn’t just lip service. Kasper maintains that “the thing I’m most proud of is our people and the management team” at Savage. He’s been part of Savage management for many years, and now that he’s sitting in the CEO’s seat, his desire is to “run the business like we used to” - look for Savage to run to the beat of the firearms market and not the stock market. It is the people of Savage Arms that were the motivating factor in getting Kasper and his group to jump into the volatile firearm market. “The immediate challenge is to negotiate through the current market turmoil (caused by the ‘Trump slump,’ bankruptcies in distribution and retail changes.”
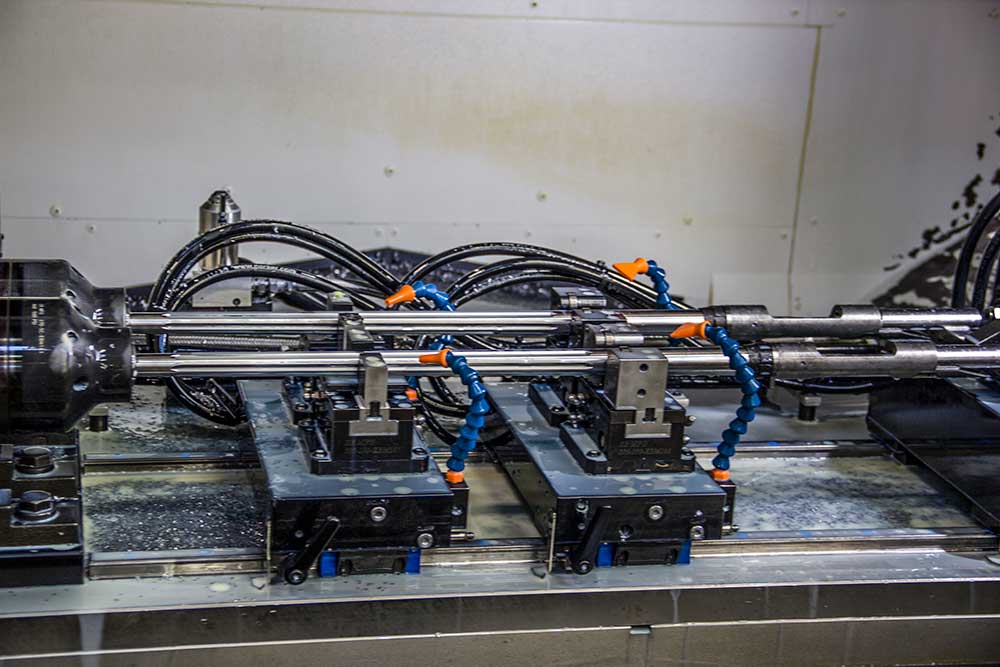
There’s more to this, too. Kasper is sensitive to the notion that Savage’s rifles are “great guns for the price” - he firmly believes the last three words shouldn’t have to be part of the praise. Savage rifles are great guns, period; anyone who’s had a chance to shoot one should agree. Touring the factory, one thing is abundantly clear: In addition to investing in people, Savage is equally committed to improving and updating the equipment used to make its rifles and components. While plenty of equipment is new, some of it is timeless, like the barrel-straightening apparatus we had the opportunity to observe. The gentleman operating the machine has two decades of experience, and his enthusiasm for his job has only increased in that time.
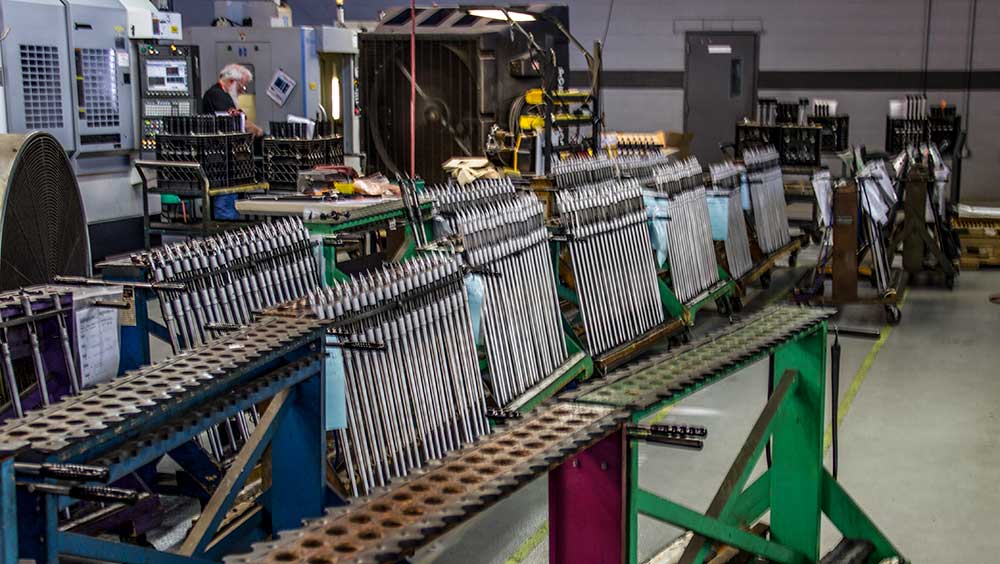
Kasper oversaw a major rearrangement of the factory workflow about five years ago, aimed at improving material flow, efficiencies and safety. His initial proposal to management came with a million-dollar price tag and was initially rejected. Later, after the rearrangement was finished and work resumed (with no missed sales), Kasper estimates that in excess of two million dollars in costs were saved.
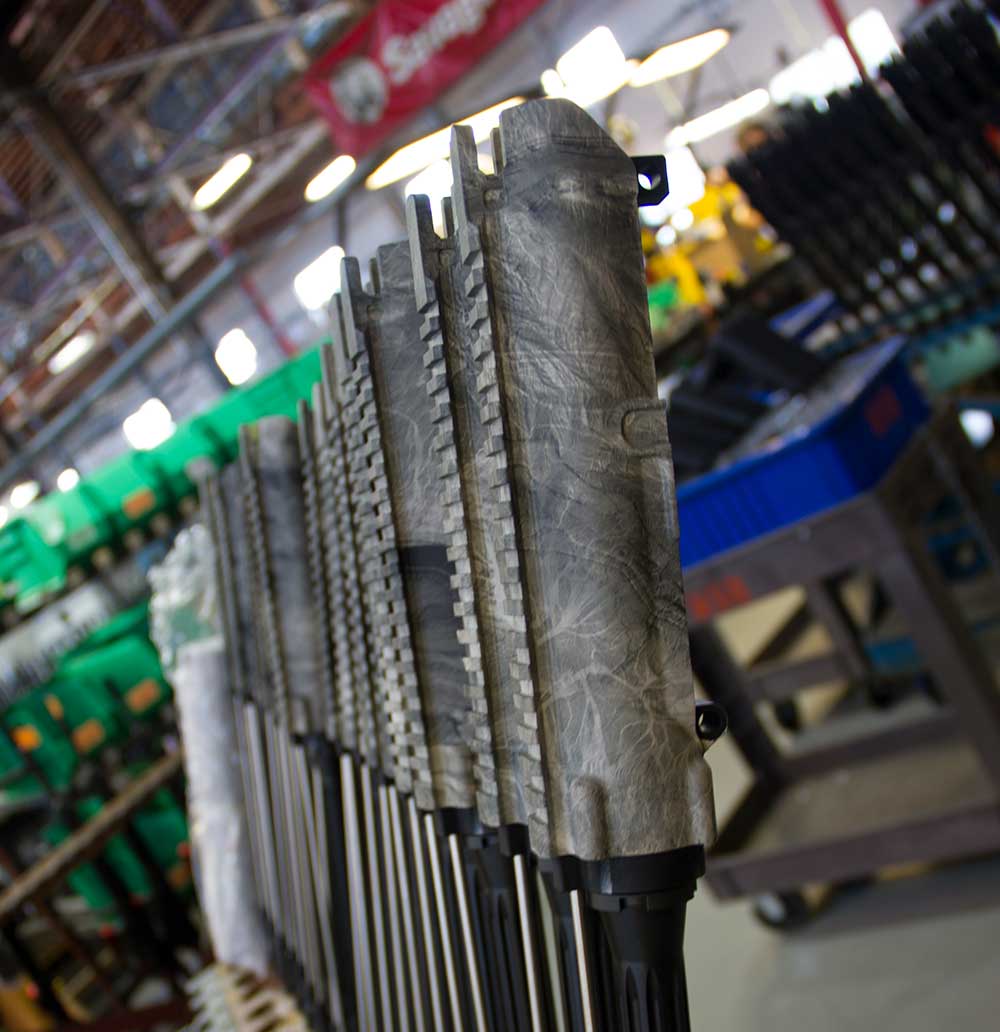
Work flow moves linearly—bar stock comes in at one end of the factory and progresses back-to-front. Barrels move in a straight line; receivers shift once for hardening. From raw materials to finished goods, everything moves in a single direction, toward packaging, with quality-control performed literally at every step of the way. Everyone who takes part in the process inspects for imperfections, from the CNC operator punching out receivers to the shipper putting paperwork in the cardboard box.
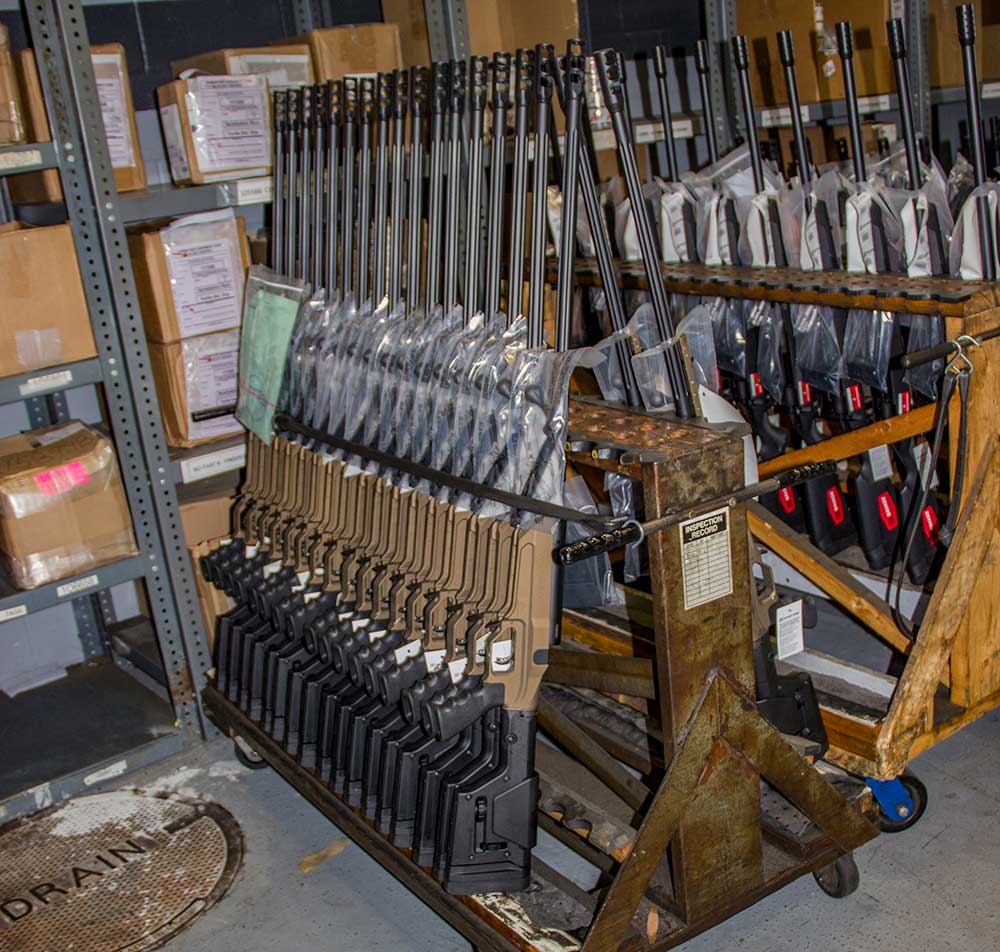
With the new leadership—that’s not really that new—keep an eye on Savage Arms for products you have not seen from the company previously. Kasper is playing new introductions close to the vest, but having seen a few of the prototypes and first-run firearms, it’s clear Savage isn’t resting on its laurels. There’s real innovation from this 125-year-old company, with plenty more to come in the coming months and years. Stay tuned to our website for more information on these new developments.