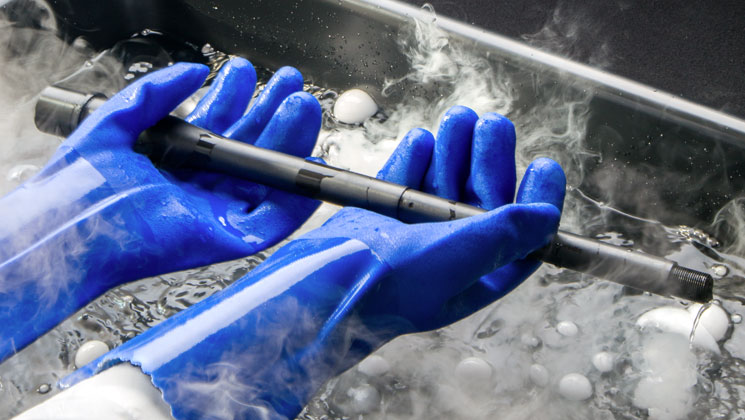
You have probably noticed rifle barrels with coating descriptions like Melonite, Ni-Corr, Blacknitride or salt-bath-nitrided are suddenly appearing on everything from rack-grade semi-autos to high-end, bolt-action rifles. They are all variations of a surface treatment formally known as “Liquid Salt Bath Ferritic Nitrocarburizing Non-Cyanide Bath,” but more commonly referred to as FNC or just plain nitriding. Tenifer, the cyanide-based original version of this process, first came to the shooting world from Austria on Glock handgun slides many years ago. Our processes differ mainly in that they use cyanate in place of cyanide but, whatever the name, it seems nitrided gun parts and barrels are everywhere these days. If you have wondered about the accuracy and durability of nitrided barrels when compared to plain stainless steel or chrome-moly/chrome-lined (CM/CL), you are not alone.
Back when AR parts were scarce, I stumbled on a batch of budget-priced, nitrided 5.56 NATO barrels. I gambled and bought five of them because I needed barrels. One barrel had a small nick in the crown and I quickly learned the FNC process makes a barrel’s surface very hard. The treated steel laughed at my hand-crowning tools, forcing me to instead use my lathe and a carbide tool to “kiss” the crown back into symmetry. All five of those barrels shot sub-MOA with multiple factory loads. Not bad for $89 each.
Recently, I consulted Steve and Stephanie Dahlke of Criterion Barrels to get their thoughts on nitrided barrels. Criterion makes fantastically accurate CM/CL barrels but they will soon offer nitrided stainless barrels in all the same contours as the company’s current lineup. Their data shows FNC yields superior stainless steel barrel properties in terms of wear, with no negative effects on accuracy. Criterion does not believe nitriding holds any advantage over its chrome-lining method on chrome-moly barrels and given its mastery of the chrome-lining process, I can understand why. One thing Dahlke pointed out is due to the different rates at which various types of steel expand when heated, the nitriding process tends to loosen up barrel extensions. So, existing AR-type barrels that are treated must have their extensions properly timed and torqued afterward.
Steve pointed me to Shade McMillen, H&M Metal Processing’s vice president and part-owner, for technical help with details of the FNC process. H&M has been nitriding an enormous range of parts since the 1980s. The company’s products run the gamut from diesel locomotive engine parts to components found on the Mars Rover. Its customers include everyday shooters with a single barrel as well as large and small firearms manufacturers with entire lines of nitrided OEM barrels and parts. Oh, and the company nitrides 3,000 to 4,000 AR barrels every day. Here is what I learned from Criterion and H&M.
Chrome-lined bores are actually coated and most companies are unable to do this uniformly. Nitriding does not add a coating, rather, it changes the surface properties by diffusing nitrogen and carbon into the metal surface to yield an extremely smooth, uniform and wear-resistant bore. Chrome-lined barrels still need outer surface protection, normally achieved by some manner of Parkerization. Since the hot liquids used in nitriding flow over all exposed surfaces in a bath, the entire barrel gets a very durable layer of protection against corrosion. A barrel that is to be chromed has to be drilled, rifled and chambered slightly oversize to account for the thickness of the chrome lining. Nitriding does not change any dimensions, so it can be applied to finished barrels.
I was surprised to learn from McMillen the only way to remove a properly nitrided treatment is to actually remove the metal. I see a silver appearance throughout when bore-scoping well-seasoned nitrided stainless steel barrels. I thought this was nitride wearing thin, but it turns out the black stuff that comes out on cleaning patches is simply “free iron” resulting from the FNC process. The surface treatment is still fully intact once the black is gone. Proper nitriding will make a chrome-moly barrel’s surface as hard as it can be made. Stainless barrels—which have otherwise been very difficult to toughen up against wear—also become much harder than normal once nitrided.
I recently compared two sets each of nitrided and untreated stainless steel barrels. The barrel configurations were identical: button-rifling, medium-contour, 16-inch, match .308 Win. chambers with mid-length gas systems. Each barrel had 100 rounds put through it using a slow break-in process. In both cases the nitrided barrels were very dirty for the first 15 rounds, but then cleaned up nicely and broke-in faster than the plain stainless steel barrels. Accuracy was the same with all barrels, averaging between .6 and .8 MOA using the same ammunition.
Afterward, the nitrided barrels did not have any traces of copper while the plain stainless steel barrels needed extra cleaning to remove all jacket material. McMillen also mentioned the more-uniform nitrided bores often yield higher velocities than do the usually rougher chrome-lined bores. I have not tested this, but I plan to in the near future. I do not have any long-term wear data for nitrided barrels, but he told me one large customer—a well-known AR manufacturer—tested some nitrided 4150 chrome-moly barrels. No loss in accuracy was noted, and no measurable throat wear was detected after more than 30,000 rounds. That is impressive.
I do not think nitriding spells the death knell for chrome-lined bores. Companies like Criterion, that can chrome a bore evenly and smoothly, are not likely to stop doing something they excel at. But most chrome linings fall short in this area, and it seems likely we will see many barrel makers start nitriding their chrome-moly barrels. In terms of drawbacks, excessive or incorrectly applied heat is the main concern when a barrel goes through the FNC process. The steel’s temperature is raised to near the same range as is used for stress relieving. If this is not done correctly—using a process known as slow quench-polish-quench (QPQ)—the steel may be warped and an inferior surface treatment could be rendered.
Some companies claiming to nitride their barrels are actually using abbreviated processes like “gas nitriding” or “black nitriding” (not to be confused with Blacknitride, which is an H&M trademark for FNC) that skip steps in the QPQ process. Unlike FNC, these methods do not leave a black finish on the barrel, so the steel must be further coated with Teflon, paint or some other finish to make them appear nitrided. It pays to make sure you are getting the real deal—SAE standard AMS-2753—when considering a nitrided barrel. I asked McMillen if there were any barrels that should not be nitrided, and he said he will not touch those that are already chrome-lined. Beyond that, untreated stainless steel and chrome-alloys are fair game.
The future looks bright for the FNC application on firearm components. If they live up to expectations in terms of wear life and performance, I expect we will see nitrided stainless and chrome-moly barrels become the rule, rather than the exception.
Back when AR parts were scarce, I stumbled on a batch of budget-priced, nitrided 5.56 NATO barrels. I gambled and bought five of them because I needed barrels. One barrel had a small nick in the crown and I quickly learned the FNC process makes a barrel’s surface very hard. The treated steel laughed at my hand-crowning tools, forcing me to instead use my lathe and a carbide tool to “kiss” the crown back into symmetry. All five of those barrels shot sub-MOA with multiple factory loads. Not bad for $89 each.
Recently, I consulted Steve and Stephanie Dahlke of Criterion Barrels to get their thoughts on nitrided barrels. Criterion makes fantastically accurate CM/CL barrels but they will soon offer nitrided stainless barrels in all the same contours as the company’s current lineup. Their data shows FNC yields superior stainless steel barrel properties in terms of wear, with no negative effects on accuracy. Criterion does not believe nitriding holds any advantage over its chrome-lining method on chrome-moly barrels and given its mastery of the chrome-lining process, I can understand why. One thing Dahlke pointed out is due to the different rates at which various types of steel expand when heated, the nitriding process tends to loosen up barrel extensions. So, existing AR-type barrels that are treated must have their extensions properly timed and torqued afterward.
Steve pointed me to Shade McMillen, H&M Metal Processing’s vice president and part-owner, for technical help with details of the FNC process. H&M has been nitriding an enormous range of parts since the 1980s. The company’s products run the gamut from diesel locomotive engine parts to components found on the Mars Rover. Its customers include everyday shooters with a single barrel as well as large and small firearms manufacturers with entire lines of nitrided OEM barrels and parts. Oh, and the company nitrides 3,000 to 4,000 AR barrels every day. Here is what I learned from Criterion and H&M.
Chrome-lined bores are actually coated and most companies are unable to do this uniformly. Nitriding does not add a coating, rather, it changes the surface properties by diffusing nitrogen and carbon into the metal surface to yield an extremely smooth, uniform and wear-resistant bore. Chrome-lined barrels still need outer surface protection, normally achieved by some manner of Parkerization. Since the hot liquids used in nitriding flow over all exposed surfaces in a bath, the entire barrel gets a very durable layer of protection against corrosion. A barrel that is to be chromed has to be drilled, rifled and chambered slightly oversize to account for the thickness of the chrome lining. Nitriding does not change any dimensions, so it can be applied to finished barrels.
I was surprised to learn from McMillen the only way to remove a properly nitrided treatment is to actually remove the metal. I see a silver appearance throughout when bore-scoping well-seasoned nitrided stainless steel barrels. I thought this was nitride wearing thin, but it turns out the black stuff that comes out on cleaning patches is simply “free iron” resulting from the FNC process. The surface treatment is still fully intact once the black is gone. Proper nitriding will make a chrome-moly barrel’s surface as hard as it can be made. Stainless barrels—which have otherwise been very difficult to toughen up against wear—also become much harder than normal once nitrided.
I recently compared two sets each of nitrided and untreated stainless steel barrels. The barrel configurations were identical: button-rifling, medium-contour, 16-inch, match .308 Win. chambers with mid-length gas systems. Each barrel had 100 rounds put through it using a slow break-in process. In both cases the nitrided barrels were very dirty for the first 15 rounds, but then cleaned up nicely and broke-in faster than the plain stainless steel barrels. Accuracy was the same with all barrels, averaging between .6 and .8 MOA using the same ammunition.
Afterward, the nitrided barrels did not have any traces of copper while the plain stainless steel barrels needed extra cleaning to remove all jacket material. McMillen also mentioned the more-uniform nitrided bores often yield higher velocities than do the usually rougher chrome-lined bores. I have not tested this, but I plan to in the near future. I do not have any long-term wear data for nitrided barrels, but he told me one large customer—a well-known AR manufacturer—tested some nitrided 4150 chrome-moly barrels. No loss in accuracy was noted, and no measurable throat wear was detected after more than 30,000 rounds. That is impressive.
I do not think nitriding spells the death knell for chrome-lined bores. Companies like Criterion, that can chrome a bore evenly and smoothly, are not likely to stop doing something they excel at. But most chrome linings fall short in this area, and it seems likely we will see many barrel makers start nitriding their chrome-moly barrels. In terms of drawbacks, excessive or incorrectly applied heat is the main concern when a barrel goes through the FNC process. The steel’s temperature is raised to near the same range as is used for stress relieving. If this is not done correctly—using a process known as slow quench-polish-quench (QPQ)—the steel may be warped and an inferior surface treatment could be rendered.
Some companies claiming to nitride their barrels are actually using abbreviated processes like “gas nitriding” or “black nitriding” (not to be confused with Blacknitride, which is an H&M trademark for FNC) that skip steps in the QPQ process. Unlike FNC, these methods do not leave a black finish on the barrel, so the steel must be further coated with Teflon, paint or some other finish to make them appear nitrided. It pays to make sure you are getting the real deal—SAE standard AMS-2753—when considering a nitrided barrel. I asked McMillen if there were any barrels that should not be nitrided, and he said he will not touch those that are already chrome-lined. Beyond that, untreated stainless steel and chrome-alloys are fair game.
The future looks bright for the FNC application on firearm components. If they live up to expectations in terms of wear life and performance, I expect we will see nitrided stainless and chrome-moly barrels become the rule, rather than the exception.